FAQs – Conversion Van Windows
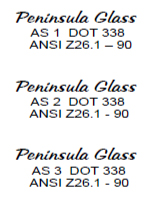
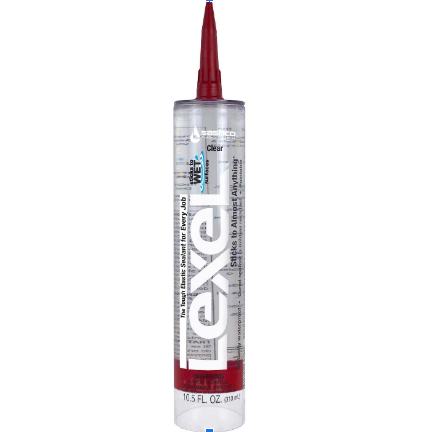
The rough opening is the hole that the window is installed in. To measure accurately, any existing window should be partially or completely uninstalled.
Wall thickness refers to the distance between the exterior and interior walls of a structure. In some cases, like an RV, the thickness can be several inches and in others like the cabin wall a boat may simply be the thickness of the metal skin. Measuring this distance is vital when installing a window, as it determines the size of the interior window frame, or trim ring, needed for proper installation.
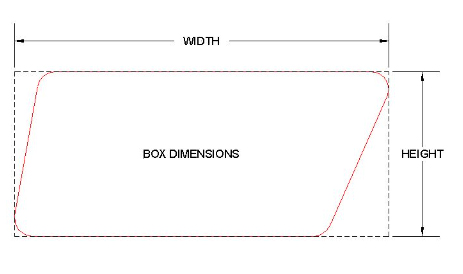
No. Everything we manufacture starts with a customer supplied Build Worksheet. While we do have some restrictions on corner radius options, almost every other aspect of creating the window is customizable to suit.
We only ship within the United States and Canada. If you need your order shipped outside of this area, you will need to contract an independent freight forwarder found within the United States for shipment directly to you. Please provide us with the name and shipping address of your preferred forwarder and we will quote your final freight charges to their location.
Credit card receipts are automatically generated by the credit card processing company and are emailed from noreply@mail.authorize.net. If you do not see a receipt, please check your spam/junk folder as emails from this address can often be misidentified.
Please follow this link: https://www.motionwindows.com/radius-template/
If included in your order, we supply a Norseal V990 Series foam glazing tape. This foam sealant combines a closed-cell polyvinyl chloride foam substrate with a pressure-sensitive adhesive on both sides for an excellent weather tight seal in a variety of land or marine applications. You can learn more about the product we supply here www.tapesolutions.saint-gobain.com.
First introduced in 1972, The Solarcool® Bronze reflective coating is a metallic oxide that is applied during the floating or cooking part of glass manufacturing. The glass floats on a tin canister into a heater under a controlled nitrogen and hydrogen atmosphere. Once the glass begins to cool, the surface is heated & polished, removing any excess blemishes. The glass ribbon is then transported to an annealing or cooling layer where The Solarcool® Bronze coating becomes permanent and uniform, allowing the glass to be heat treated to satisfy increased strength or safety glazing requirements.
The metallic sheen on the exterior coated piece of glass will also function as a layer of UV protection, reflecting nearly 40% of solar heat away from your application. Creating an indoor space that will stay cooler & brighter much longer, in comparison to any uncoated glass.
Extra Care is Required
- Wash periodically using only soft, clean, grit-free cloths and mild soaps or detergents. Avoid acidic cleaning solutions, fluorine salts, hydrogen producing compounds, or abrasive cleaners as these may damage your new windows exterior coating.
- Immediately after washing, the entire surface should be rinsed with clean water, and a soft squeegee, blower, or microfiber should be used to remove excess rinse water.
- If your application is positioned where weathering can be a risk, it should be washed more often to remove deposits that may exist on the glass.
At our company, we've redefined the window manufacturing industry by embracing a unique approach. Unlike traditional manufacturers who stick to standard sizes and limited stock, we recognized a gap in the market for a more versatile and customer-centric offering.
Our ethos is simple: empower customers with unprecedented freedom of choice. We boast an expansive product range encompassing sliding and fixed styles, accompanied by an extensive selection of glass tints and powder coat frame colors. This breadth of options allows us to cater to diverse tastes and styles, ensuring that each customer finds the perfect fit for their needs and preferences.
By prioritizing customization and variety, we've established ourselves as leaders in the industry, setting new standards for excellence and innovation. Welcome to a world where your imagination sets the limits, and we're here to bring your vision to life.
As a custom manufacturer our lead times can vary between 30 to 90 days throughout different points of the year. Typically, peak season for our land vehicle line begins in early spring and extends into summer and our marine segment’s busiest season runs fall into early winter. We provide an estimated manufacturing time frame with each individual quote we provide.
Remove the existing window(s) entirely. Your pattern material should be made of heavy-duty construction paper, 1/8” plywood or equivalent. Use a new Sharpie.
Retrieve your packing list by following this link https://peninsulaglass.com/packing-list/. You’ll need your order number and email address associated with your account.
Our warranty covers defects in material and workmanship for 2 years from the original purchase date. Within this period, we will repair or replace defective parts at our discretion, with the customer responsible for return shipping costs. Original shipping costs are non-refundable. Corrosion defects in powder-coated windows installed in saltwater marine conditions are covered. Exclusions include improper installation, misuse, abuse, or neglect, and warranty is void if disassembly or service is conducted by anyone other than Peninsula Glass after installation. Warranty claims require proof of purchase and contact with Peninsula Glass for assessment. Our liability is limited to repair or replacement of defective parts, with no liability for incidental or consequential damages. The warranty is non-transferable and applies only to the original purchaser. Contact us for inquiries or claims.